Compressed Air System Filtration and Separation
Compressed air must be free of aerosols, oil and particles, and liquid water before being used in your application. During compressed air generation and distribution, contaminants are introduced to the air stream at various stages of the compressed air network. Compressed air filters, which come in various grades, along with separators will remove these contaminants, as well as humidity, oil, and bulk water from the compressed air stream. This is a critical step as these contaminants can lead to a deterioration in quality, machine failure, or even to a loss of production or to products that must be disposed of. CLEARPOINT® compressed air filters and water separators ensure the purity of your compressed air – safely and efficiently.
CLEARPOINT® Compressed Air Filters
During compressed air generation and distribution, contaminants are introduced to the air stream at various stages of the compressed air network. Compressed air filters, which come in various grades, remove these contaminants, as well as humidity and oil from the compressed air stream. This is a critical step as these can lead to a deterioration in quality, machine failure, or even to a loss of production or to products that must be disposed of.
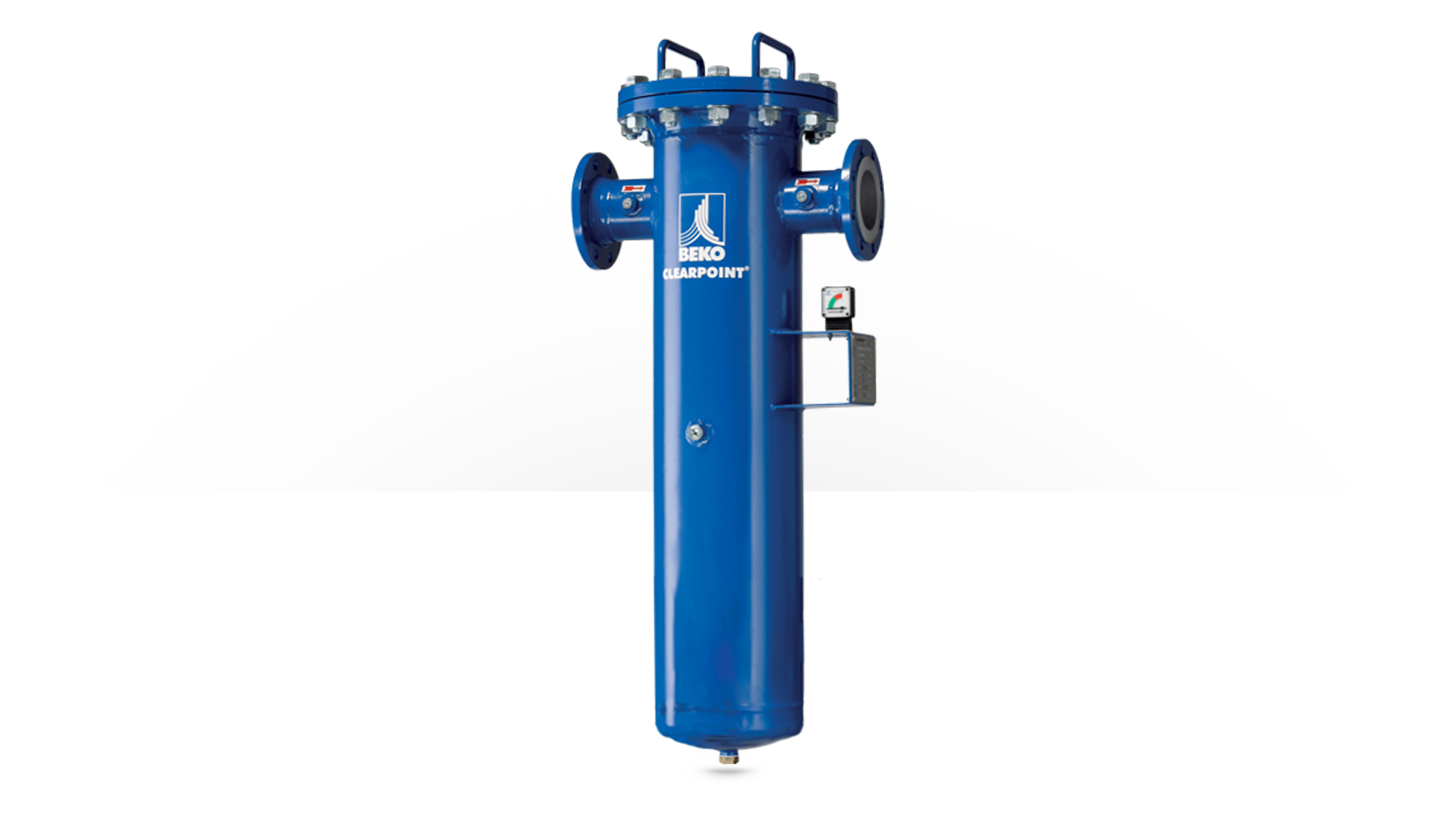
CLEARPOINT® Water Separators
In-line water separators are typically used at after coolers and refrigeration dryers in order to remove bulk liquid that is present in the compressed air pipework as a result of condensate being formed. All compressed air systems create some level of condensate through the basic function of compression. Poor water or condensate management can result in process contamination, component failure, and high differential pressure. All of which can be very costly when compared to the cost of removal.
CLEARPOINT® In-line Heaters
Our CLEARPOINT® H series of in-line heaters are the perfect solution for applications with frost-prone pipes or where stable compressed air temperatures above room temperature is required. The temperature range is user adjustable between 86 °F and 140 °F making them extremely versatile in a variety of applications.