Instrumentation for Compressed Air Systems
The precise measurement of humidity, hydrocarbons, flow, temperature, and pressure provide the foundation for various analyses, documentation, and decisions as they relate to compressed air systems. Potential overload (e.g. excessive air velocity) or malfunctions can be detected early, quickly, and reliably, which allows for the most precise and economical optimization of all plant components. The use of superior quality, industrial grade measurement equipment eliminates all the guesswork.
METPOINT® Monitoring Systems
One can measure quality – one just needs to record it. The data logger from the METPOINT® BDL series translates process data into easily understandable statistics and graphics. You can comprehend the measured values simply and in real time and immediately implement the necessary measures as they are needed. Available from anywhere, at all times – due to complete network capability for worldwide and system overarching data transfer.
METPOINT® Sensor Technologies
Residual moisture, pressure, volume flow, hyrdrocarbons, leaks: all major factors for more efficiency in your production processes. The various sensor technologies from BEKO TECHNOLOGIES enable you to precisely record all the relevant parameters at all critical control points for your compressed air - your basis for energy and cost-saving decisions You can therefore prevent possible malfunctions, reduce the escape of expensive compressed air, clearly allocate costs to individual production processes, and specify and optimize the components of your production facilities for the best possible economical results.
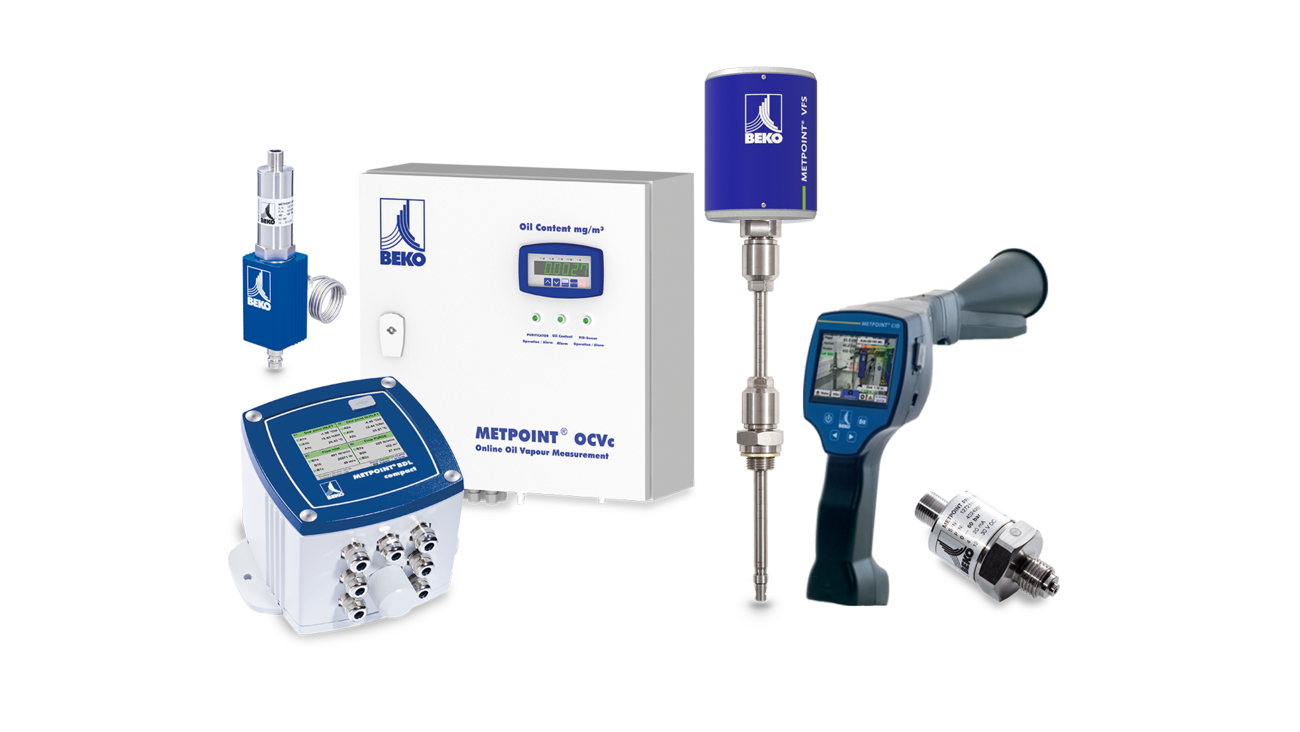
METPOINT® Portable Instrumentation and Monitoring
Residual moisture, pressure, volume flow, leaks: four key factors for more efficiency in your production processes. The sensor technology from BEKO TECHNOLOGIES enables you precisely record all the relevant parameters at the critical control points for the compressed air - your basis for energy and cost-saving decisions You can therefore prevent possible malfunctions, reduce the escape of expensive compressed air, clearly allocate costs to individual production processes and dimension and optimise the components of your production facilities for the best possible economical results.
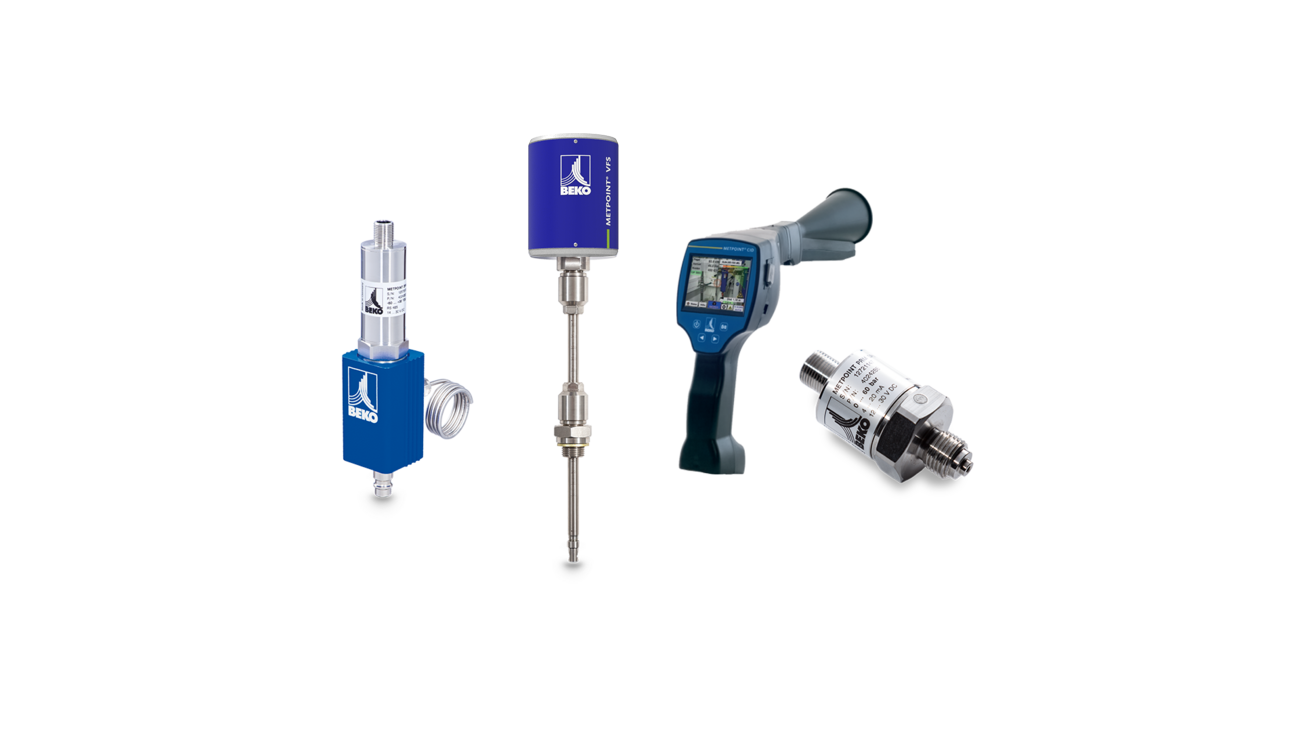